How to Choose the Right Valve Bag-Making Machine for Your Business?
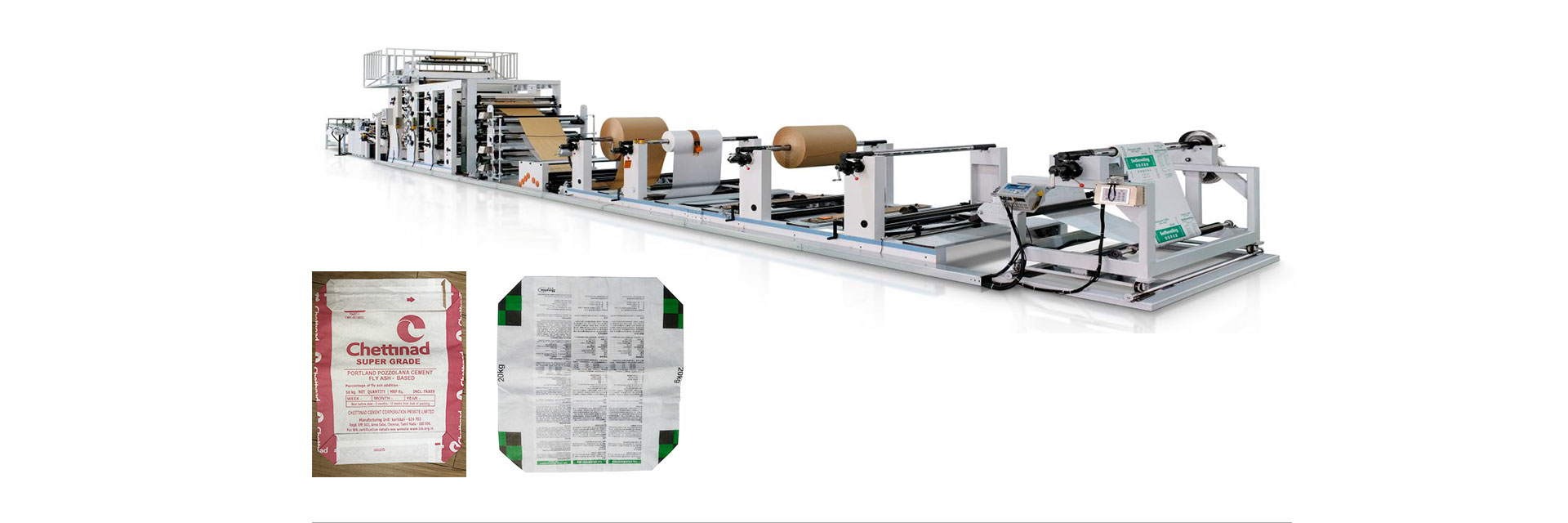
1. Bag Size and Capacity
One of the first considerations is the size and capacity of the bags you need to produce. Different machines are designed to handle various sizes and weights of bags. Some machines can produce small, lightweight bags, while others are capable of making large, heavy-duty bags. It's important to choose a machine that matches your specific requirements in terms of bag dimensions and production volume. Assess your production needs to ensure the machine can meet your output demands without compromising on quality.
2. Type of Valve
The type of valve used in the bags is another critical factor. There are several types of valves, including open-mouth, self-sealing, and pinch-bottom valves. The choice of valve depends on the nature of the product being packaged and the specific needs of your business. For instance, self-sealing valves are ideal for products that need to be tightly sealed to prevent contamination, while open-mouth valves are suitable for products that require easy access.
3. Material Compatibility
The thickness and composition of the materials used to make the bags are essential considerations. Valve bag-making machines can handle various materials, including paper, plastic, and woven fabrics. Each material has its unique properties and applications. For example, polyethylene (PE) is known for its moisture resistance, making it suitable for packaging products that need protection from humidity. Polypropylene (PP) is lightweight and strong, ideal for chemical and agricultural products. Ensure that the machine you choose is compatible with the materials you plan to use.
4. Speed and Efficiency
The speed and efficiency of the machine are vital for meeting production targets. The production speed will determine how many bags can be produced in a given period, while efficiency will affect the overall productivity and waste generation. Choose a machine that offers a balance between speed and quality, ensuring that it can produce bags quickly without compromising on the integrity of the seals or the accuracy of the cuts.
5. Accuracy and Precision
Accuracy and precision are crucial, especially for products that require exact measurements and consistent quality. Some applications demand high accuracy, while others may allow for some variance. Evaluate the level of precision required for your filling process and select a machine that can meet these standards. High-precision machines may come at a higher cost but can significantly reduce waste and improve product consistency.
6. Maintenance and Support
Maintenance and support are important factors to consider for the long-term operation of the machine. Opt for a machine that is easy to maintain and repair, with readily available replacement parts. Comprehensive support, including technical support and training for operators, can minimize downtime and ensure smooth operation. Machines with complex or hard-to-find parts can lead to prolonged downtime and increased maintenance costs.
7. Cost and Budget
The cost of the machine is a significant consideration. Different machines come with varying price tags, so it's essential to choose one that fits within your budget. However, it's also important to consider the long-term costs associated with the machine, including maintenance, repair, and replacement parts. Investing in a high-quality machine may have a higher upfront cost but can lead to savings in the long run due to reduced downtime and maintenance expenses.
8. Safety Features
Safety should always be a priority when selecting machinery. Look for machines equipped with safety features such as emergency stop buttons, safety interlocks, and guarding to protect operators during operation and maintenance. Ensuring a safe working environment can prevent accidents and improve overall productivity.
9. Dust Control and Containment
For businesses dealing with dusty materials, dust control is crucial. Machines with dust collection systems and sealing mechanisms can minimize dust emissions, ensuring a clean and safe working environment. Effective dust control can also improve the quality of the packaging and reduce the risk of contamination.
10. Flexibility and Versatility
Consider whether the machine can handle a variety of products or if it is designed for a specific type of material. A versatile machine can be more cost-effective in the long run, allowing you to adapt to different packaging needs without the need for multiple machines.
Conclusion
Investing in the right valve bag-making machine is a strategic decision that can significantly impact your business's productivity and profitability.
Choosing the right valve bag-making machine involves careful consideration of various factors, including bag size and capacity, type of valve, material compatibility, speed and efficiency, accuracy and precision, maintenance and support, cost and budget, safety features, dust control, and flexibility. By evaluating these factors and aligning them with your business needs, you can select a machine that enhances your packaging process, improves efficiency, and ensures product integrity.