Sincere service impresses customers
A truck slowly entered the factory of Foshan Tecon Package Machinery Co., Ltd at noon. There is more than 5,000 paper tubes in the truck, which is ready to produce valve paper bags. The workers skillfully removed the tubes from the truck and placed them neatly on the head of the new Bottomer Machine.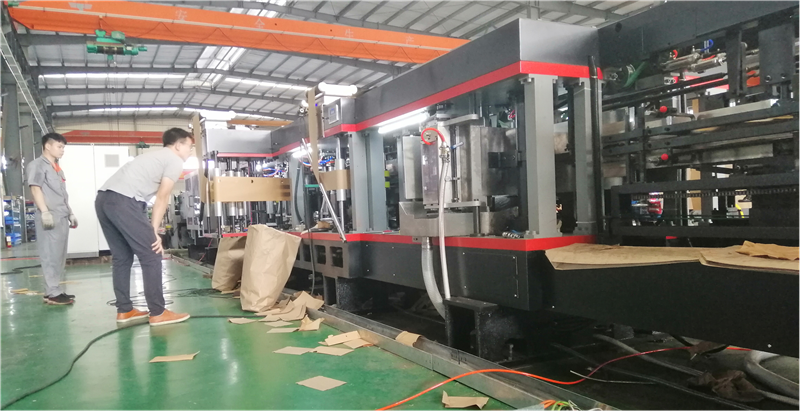
The customer purchased a complete valve paper bags production line fro another supplier. He has a lot of orders from his customer, he need the production line to produce valve bags with good quality immediately. However, it is a new factory has just been established, he didn’t want to invest too much on the equipment. He knows that the quality of the equipment from Tecon Company is very good, but expensive, Thought repeatedly, and finally chose the cheap production line. The customer complained that the equipment has been bought for several months and has been unable to produce qualified products. Although the Tuber Machine can stably produce the tubes, but the speed is not fast, the size is not accurate enough, the deviation is large. Yes, it is acceptable, because the equipment is cheap. The bad is, the Bottomer Machine even is not workable. His technicians try their best to commission the machine for long time, but still not can produce qualified valve bags. He wasted a lot of time and money, also seriously affected his business. He suffered a lot on it.
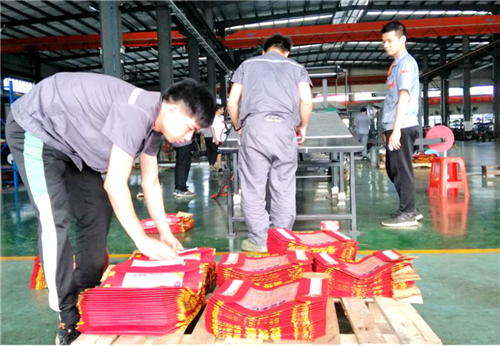
There is really no other way to solve the problem. So, two young guys, the bosses of the company came to Tecon Company several times to discuss and learn how solve the problem. They hope that Tecon Company can provide a good solution. In a serious and responsible attitude, the Tecon company's boss sent the technical team several times to the customer's factory for actual inspection and verification. After returning to the company, they organized technical seminars to find the best solution for the customer, and finally proposed the solution as follows:
1. Make reasonable modifications to the customer's existing Tuber Machine, reduce the dimensional deviation of the tubes, correct the position of the glue, improve the flatness of the tubes, and increase the speed;
2. Because the Bottomer Machine that was purchased before is too bad quality, it is impossible to carry out technical upgrading and upgrading, so suggest the customer to carry about 5,000 tubes which produced in his factory to test in Tecon's Bottomer Machine to see whether it can produce qualified valve bag . If it can, that means the Tuber Machine can match the Tecon Company’s Bottomer Machine, then the customer will buy a bottom machine from Tecon Company.
So, today, what is why we saw the scene at noon, the customer took his own tubes into the Tecon Company's workshop. The quality of the tubes produced by the customer was not very good. Customers expect a trial production capacity of 60 / min. The Bottomer Machine in Tecon Company workshop is already purchased by another customer. After tested for this customer will uninstalled and delivered to the customer. The similar size of the bags has been stably run at 120 bags/min during the trial production before. However, considering this customer's tube size is irregular, the deviation is big, the quality of the tubes are not good, so the technical staff of Tecon Company stabilized the test speed at 70 bags/min.
The two bosses, measured in size and quantity of the bags, which produced on the Tecon Company's Bottomer Machine. They checked one and another, looks very carefully and seriously, because of the previous experience. In the end, they were very satisfied and decided to buy a Bottomer Machine from Tecon Company.
Because the customer accumulated a lot of orders, in a hurry, eventually reached an agreement with Tecon Company to order a bottom machine that will be upgraded with the latest technology in an old Bottomer Machine, which is laying already in workshop. The customer has placed an order and is expected to deliver at the end of July.