Valve Bag Making Machines
In the world of packaging, efficiency, versatility, and reliability are paramount. And among the many machines that cater to these needs, the valve bag-making machine stands out as a cornerstone in the packaging industry. Why they're indispensable in modern packaging operations? Read on to know more.
Understanding Valve Bag-Making Machines
At its core, a valve bag-making machine is a specialized device designed to fabricate valve bags—a type of packaging characterized by a one-way valve mechanism.
These machines operate by taking raw materials, typically plastic films or woven fabrics, and transforming them into precisely shaped bags with integrated valve mechanisms.
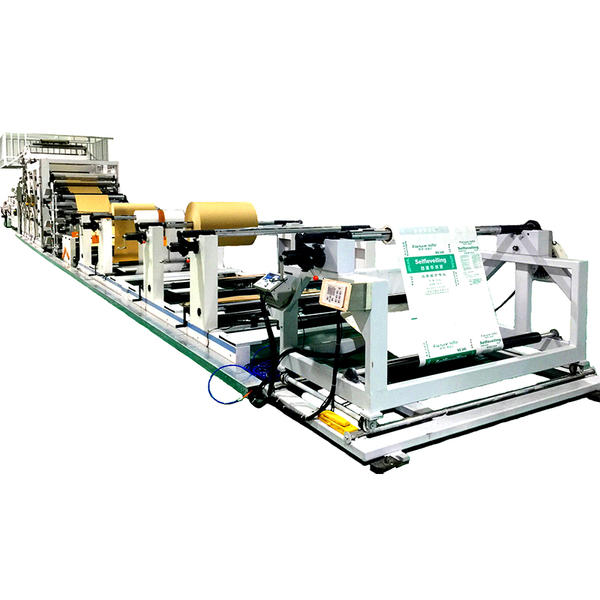
Mechanisms and Components
Key components of a valve bag-making machine include a material feeding system, sealing unit, cutting unit, and valve applicator.
Material feeding systems ensure a continuous supply of raw materials, while the sealing unit employs heat or pressure to create secure seals.
The cutting unit precisely cuts the material into desired bag shapes, and the valve applicator affixes the valve mechanism onto the bags.
Versatility in Materials
Valve bag-making machines are capable of working with various materials, including polyethylene, polypropylene, and woven fabrics.
This versatility allows manufacturers to produce bags tailored to specific requirements, whether it's for packaging chemicals or construction materials.
Applications Across Industries
Valve bags find applications in diverse industries such as agriculture, chemicals, construction, and food.
In agriculture, valve bags are commonly used for packaging fertilizers, seeds, and animal feed due to their durability and moisture resistance.
In the chemical industry, valve bags provide a reliable containment solution for powdered or granular substances, ensuring safe handling and transportation.
Similarly, in the food industry, valve bags maintain product freshness and integrity, making them ideal for packaging coffee, flour, and pet food.
Efficiency and Cost-Effectiveness
Modern valve bag-making machines come equipped with advanced features that allow for customization and innovation. From adjustable bag sizes to customizable printing options, manufacturers have the flexibility to meet specific branding and packaging requirements.
Valve bag-making machines offer significant efficiency gains compared to manual bagging processes. With automation, these machines can produce large volumes of bags consistently and quickly, reducing labor costs and increasing overall productivity. Additionally, the precise control over material usage minimizes waste, contributing to cost savings in the long run.
Maintenance and Support
Valve bag-making machines adhere to stringent safety standards to ensure operator well-being and product integrity. Safety features such as emergency stop buttons, interlocking guards, and automated shutdown mechanisms mitigate potential hazards in the production environment. Compliance with regulatory standards ensures that the bags produced meet quality and safety requirements for their intended applications.
Regular maintenance is essential to keep valve bag-making machines operating at peak performance. Maintenance tasks may include cleaning, lubrication, and inspection of key components to prevent downtime and prolong the machine's lifespan. Many manufacturers offer comprehensive support services, including training programs and technical assistance, to help operators maintain and troubleshoot their equipment effectively.
Conclusion
Valve bag-making machines epitomize efficiency, versatility, and reliability in the packaging industry. From their intricate mechanisms to their diverse applications across industries, these machines play a vital role in streamlining packaging operations and ensuring product integrity. As technology continues to evolve, so too will the capabilities of valve bag-making machines, further cementing their status as indispensable assets in modern manufacturing processes.